Organisations which prioritise the continual improvement and innovation of their existing practices often use Lean[1] processes such as Continuous Improvement (CI) cells[2].
Continuous Improvement cells are a work improvement technique, which originated from the concept of Quality Circles[3]. The main benefits of adopting this approach can include productivity improvement, cost savings, safety improvements, workforce engagement and work quality improvement, all of which can lead to significant benefits for industry.
Working with industry
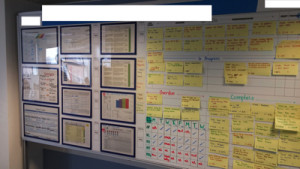
The Innovative Design Lab Research Centre (IDL) at the University of Huddersfield focuses on solving real world problems by working with organisations to develop solutions to design challenges and project based problems.
In 2016 IDL researched the benefits and challenges of Continuous Improvement cells with four organisations: Highways England, a design service supplier, a construction service supplier from the highways supply chain and Network Rail. The research was funded by Highways England.
Impact of CI cells
The research identified many benefits of CI cells at Highways England, in the highways supply chain and at Network Rail. These include improvements in team and supply chain coordination; team building and coaching; and task and resource management. Particularly significant statistics include 165% improvement in the mean staff engagement scores when comparing Highways England’s outstations which use CI cells with those that do not. A 14% productivity increase in one team was estimated based on their planning reliability records after their CI cell implementation.

The research also revealed a number of challenges, in the area of systematic data recording prior to adoption of the technique, knowledge about what to measure, standardisation and implementing continuous improvement.
Improving CI cells in the Highways Supply Chain
The research team developed a series of suggestions based mainly on the challenges they identified with current practices:
CI cell training: basic Lean training was recommended in order to raise awareness as well as introducing standard terminology and practices.
CI cell execution: in order to improve this particular aspect a number of suggestions were made, including systematic problem solving and standardising CI cell board design and execution.
CI cell benefit recording: a set of measures can be introduced so that teams know exactly what to record and measure and a better comparison is made across the board
CI cell incentivisation: in order to keep teams’ focus on continuous improvement it was suggested that an incentivisation programme between and within teams could be introduced.
Future CI cell research
Continuous Improvement cells by their very nature are always looking for new ways to improve processes and remove constraints to delivery. As part of this research IDL recommended further research, which included identifying the critical success factors by investigating why some teams are successful and others are not. Further understanding of which factors lead to better job satisfaction and evaluating how the programme could be improved were also recommended. Comparison of the performance over a period of six months of at least two similar teams, one using CI cells and the other not and evaluating the impact on their KPIs (key performance indicators) and team engagement is a future research opportunity, along with investigating where teams are allocating their saved resources through their CI cell practices and how they are being used.
Lucia Fullalove, Lean Collaborative Research Manager at Highways England who funded the research, commented:
“It is important to ensure that results from the Lean Collaborative Research are tried and incorporated into the work practices so that benefits identified by the research work can be fully realised. This will reinforce the usefulness of the research in supporting delivery of the Lean contribution to the RIS (Roads Investment Savings) at Highways England.
“Indeed, it is my experience with work in the HE Supply Chain (e.g. Manchester Smart Motorway) that all areas where I witnessed CI cells deployment have demonstrated improvements in the areas identified in the research. In addition, team members felt empowered and as a result were more pro-active in taking necessary actions to remove constraints identified in their work activities to improve or allow timely work delivery.”
[1] Alarcón, L. (1997). Lean construction. CRC Press.
[2] Miron, Luciana, Talebi, Saeed, Koskela, Lauri and Tezel, Algan (2016) Evaluation of Continuous Improvement Programmes. In: 24th Annual Conference of the International Group for Lean Construction, 18th – 24th July 2016, Boston, USA. (http://iglc.net/Papers/Details/1287/pdf)
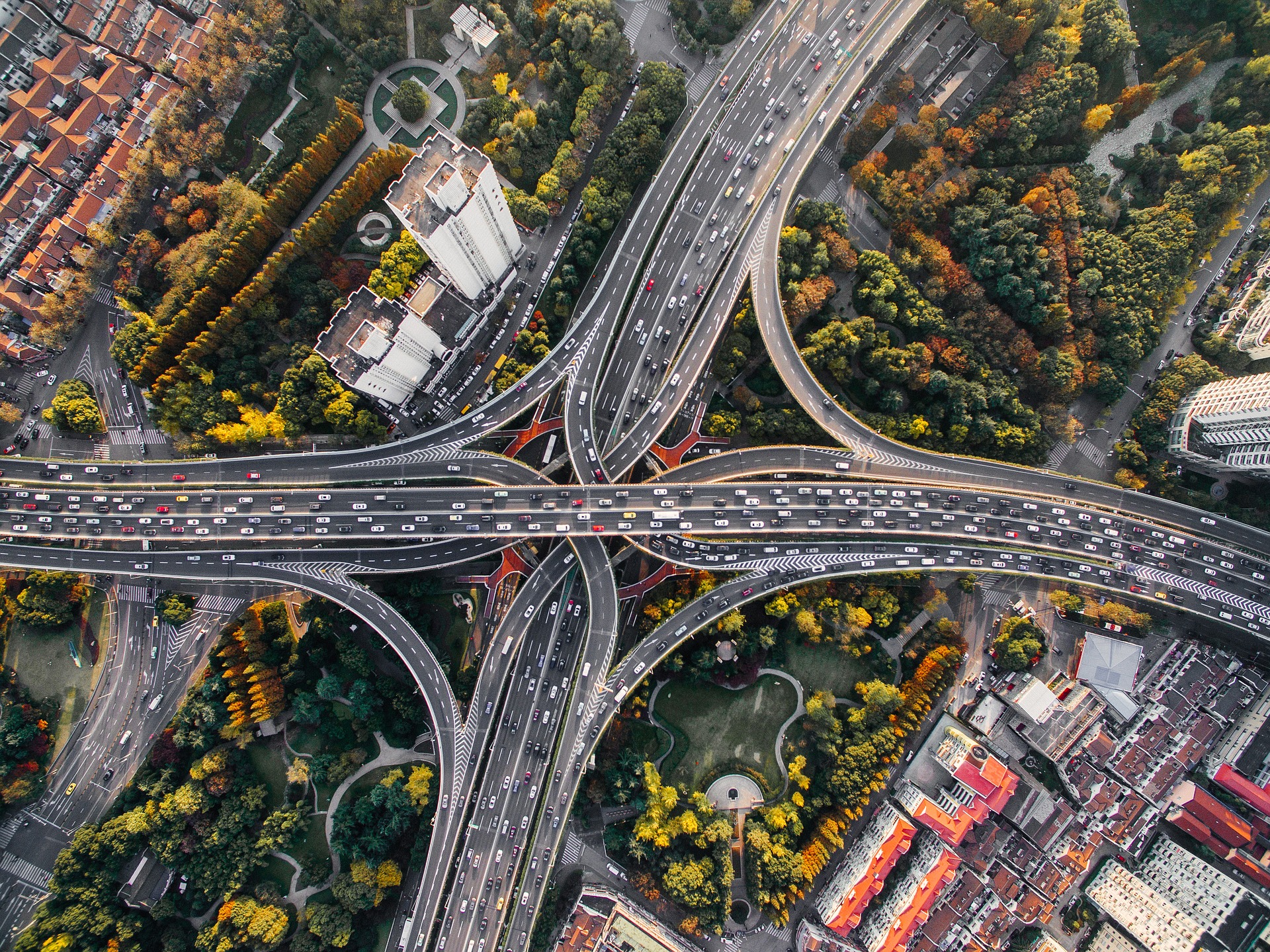
Spotlight
Innovative Design Lab Research Centre (IDL)
IDL is a new interdisciplinary research centre/laboratory at the University of Huddersfield. The lab conducts theory based and applied research generally into product design, and especially in the built environment, pushing the impact of design thinking and practice to new areas. It cuts across the areas of architectural design, construction management, interior design, new product development, engineering, social sciences and healthcare. The research focuses on solving real world problems through design innovation, mobilising the underlying theories as well as the enabling processes and technologies needed to deliver value to users and the society at large. The research is developed closely with diverse public and private sector organisations to propose novel solutions to design challenges and project based problems. To find out more about this area of research visit: Innovative Design Lab
Summer 2017 Issue
Return to the home page for the Summer 2017 Issue of Discover.
Next article
One particular problem that is raised regularly by those working to stop the illegal trade in endangered species is sentencing.